Sam and I have been friends for about 5 years. He heard I worked on classic Renaults, and wanted a few things done on his Silver V85. I did quite a bit of work for him, a real tune up and re-set all the front suspension (mod the accident damaged LH front) He was very chuffed and has returned numerous times for services and small stuff. But every time we sit and have a coffee and talk A110, and where he wants to go with it.
Sam was a regular visitor while the Gordini was being built, and asked about many things I was doing, in particular playing with a Gordini motor. When the car was in the testing stage, I took him for a drive in it, driving rather moderately, but with the occasional foot to the floor in 2nd and 3rd. He obviously was impressed.
In the last stages of a few upgrades from old parts on the Gordini, Sam came to visit, and we had a lengthy discussion with pen to paper, of a rebuild of the A110, with a strong 1600 807 and a 5 speed big box. I told him of a recently built 330, with 385 crown and pinion and 365 gears, built by Steven Swan. He went and haggled, and came back the next day telling me to pick the gearbox up.
And so started the re-build of the A110
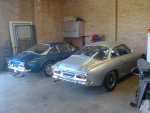
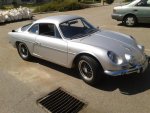
Sam was a regular visitor while the Gordini was being built, and asked about many things I was doing, in particular playing with a Gordini motor. When the car was in the testing stage, I took him for a drive in it, driving rather moderately, but with the occasional foot to the floor in 2nd and 3rd. He obviously was impressed.
In the last stages of a few upgrades from old parts on the Gordini, Sam came to visit, and we had a lengthy discussion with pen to paper, of a rebuild of the A110, with a strong 1600 807 and a 5 speed big box. I told him of a recently built 330, with 385 crown and pinion and 365 gears, built by Steven Swan. He went and haggled, and came back the next day telling me to pick the gearbox up.
And so started the re-build of the A110
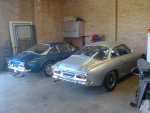
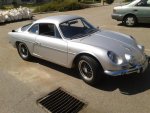