It's about time I posted a bit of a blurb on how converting the 604 to Megasquirt EFI has gone.
For the last 20 years or so the car had run a Holley 320 carburettor -- an improvement on the Solex setup, but nothing to get excited about. It now has a Megasquirt II ECU running MS2/Extra firmware controlling an EA Falcon dual throat throttle body injector. Feedback is from an Innovate LC-1 wide band controller with a sensor fitted in the LHS pipe. At the back I have a 505 fuel pump drawing through a cartridge type 10 micron fuel filter.
Doesn't sound like it'd be all that much work, but the Devil's in the details and the job has called for more than a few moments of musing how to make things work or make them fit. On the whole though, I'm very happy with progress, though there are still a few things to sort out yet.
So, here are some photos and a bit of running commentary.
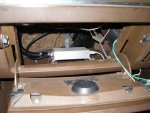
Megasquirt behind the glovebox
The photo is foreshortened, and doesn't get it across, but the MS is mounted on a cradle I made and is waaay far away. There is plenty of room for the original cardboard glovebox to slot back in. You can see the main MS DB37 electrical connector on the left, and the MAP sensor vacuum line looping around it. On the right is the RS-232 connector. The brown wire is the spare analog output from the wideband which I might hook up to an AFR gauge (maybe fit in the ashtray slot which, being built to accommodate French smokers' tastes, would easily be large enough for two gauges).
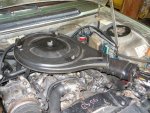
Engine bay overview
Engine bay with everything in its proper place looks reasonably stock. The Ford air cleaner doesn't look out of place and the wiring isn't too much of a rat's nest. Mind you, the Ford air cleaner took quite a bit of adapting to fit. The Ford TBI was towards the front of the engine bay. Since the 604's second carb was mounted near the back, just turning the filter around and relocating the snorkel was my original plan, but the filter ended up at a crazy rakish angle when I tried it. So it was a cut and reweld job which worked out OK (as long as you don't look too closely).
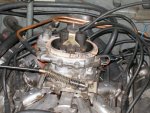
TBI detail
I've mounted the TBI on a bit of 1/4" stainless plate with four studs. This plate bolts to the previous Holley adaptor plate which in turn mounts to the manifold through four recessed allen screws. This two plate arrangement was necessary as the Solex and TBI mounting holes overlap but don't coincide. This sandwich has left the top of the air filter pretty close to the bonnet. I haven't measured with plastigage (OK plasticine); it's not rubbing but it's close.
I bent up 5/16" copper pipe to feed fuel and take away return. The thing flows like a garden hose, so there is plenty on tap. You can see the two injectors front and centre. There are two TPS sensors on the other side. Only using one; I guess the Falcon uses the other for something like idle feedback or some such. Throttle was a bit of a conundrum. I ended up using the original Falcon ball and socket connection so I could use the compression return spring. Rigging up an extension spring for throttle return didn't look straightforward ('cause it needed to go round a corner). The throttle stop is the somewhat jury rigged bit of steel mounted on RHS in the photo. Could do with a bit of stiffening up.
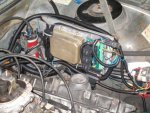
Relay board detail
Left to right we have a shiny red Bosch GT40 coil, then, mounted on a bit of bathroom trim aluminium, Innovate LC-1 controller, Bosch electronic ignition trigger box (ex Volvo) and Megasquirt relay board which gives a single point to draw all connections together. At the bottom of the relay board you can see the DB37 connector which sends a chunky cable through the firewall to the ECU. The knot of wires further to the right is the relay and thermostat for the cooling fan which has been on the car for years. Will probably get the MS controlling this and get rid of the old thermostat.
The Bosch coil seems to deliver enough sparks for me and has no bother starting the car. The ballast resistor had been playing up so a full 12V coil took that out of the equation. I have a spare Volvo dizzy and may lock it up and use the MS for full ignition control to see how that goes.
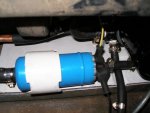
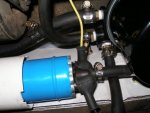
Fuel pump/filter
Two shots of this because I was too lazy to jack the car up and snap from further away. This is on the LHS in front of the rear crossmember behind the rear passenger footwell. I made up a mild steel mounting plate and drilled holes to mount it to the footwell. Then I was able to position everything on the bench without having to lie under the car.
On the left is a large copper pipe feeding a 1/2" hose to the inlet of the pump. The fuel filter is the shiny black thing on the right. Somewhat unconventionally, the pump draws through the filter which allows the filter to do double duty as a surge tank. I did this because I didn't want to be fitting a 1/2" outlet to the fuel tank. The pump requires a large inlet because it uses the fuel for cooling. The worry was that the fuel would get hotter and hotter... but that doesn't seem to eventuate (phew). There are four connections on the filter: from tank, to injector, injector return, return to tank. I didn't use the original tank return line because it (strangely) returns at about the 1/3 full level in the tank. I sent the return up to the breather at the top of the tank and have a check valve in the line so we don't draw air down this line. Since the return line should mostly be returning air accumulated at the filter, this seems satisfactory.
The fuel pump plumbing was in many ways the most complicated part of the setup. Pretty happy with it though. Despite the apparent tangle of hoses, nothing is actually rubbing on anything else and, in the flesh, it doesn't look any worse than the 604TI's pump and filter arrangement in the workshop manual.
Not pictured is the coolant temp sensor (tucked in to the valley in place of an existing temperature based vacuum switch), or the air temp sensor (a thermistor put in a drilled out old plastic medicine bottle, cable tied behind the front bumper).
So, how does it go? To begin with, I was astonished that, not only did it start first time, but it idled (at a very lumpy 450rpm or so). Definitely a promising beginning. I haven't yet finished tuning (waiting for the Christmas madness on the roads to abate), but the car has already been transformed. It still has all the stately graces a 604 should have, but the old dead areas of unresponsive throttle have gone. If you move your foot on the throttle, you are left in no doubt that the engine has got the message. Of course it's still no fire breathing monster, but it is really pleasing to feel it so responsive.
The other thing about the performance is that it's willing when cold (well, overnight in Sydney isn't exactly cold at the moment, but the car certainly used to be sluggish untill fully warmed up).
It'll be a while before I have economy figures. Obviously the consumption isn't going to be at its best while I'm tuning, but I'm hopeful that the economy will be very much better with mod cons like EGO feedback to help it out.
Problems
Yes there are still several problems to iron out. The biggest problem is the noise from the fuel line. Because I'm drawing through the fuel filter, there is just a 2" length of hose between the pump and the original steel line which is mounted direct to the floorpan. Every little pulse from the pump is turned into magnificent high fidelity sensurround sound with the passenger compartment making a wonderful soundbox. For the moment, I've left the fuel lines dangling, still noisy, but at least the banshee is a bit less amplified. My plan is to put a blind vertical pipe between the fuel pump and the fuel line This pipe will have air at the top which should work as a poor man's (or cheapskate's) accumulator, evening out the pulses. Kinder to the fuel line, and to my ears.
Probably the next biggest problem is the throttle throw. Having mounted the cable to the ball/socket connector, it only needs to move about half as far as the old Holley did. Consequently, the pedal is about 1 1/2" from closed to wide open. This has already led to a couple of cases of unwanted wheelspin, which is just not in keeping with the 604 image. I plan to move the pedal pivot up a couple of inches to increase the throw, but it's acceptable for driving at the moment.
I'm running full manifold vacuum (not ported vacuum) to the distributor advance unit. This seems to be working OK and I haven't had problems with pinging on take off. The engine does seem to stay cooler too, but I'm keeping a watching brief on this score.
The other problem is a whistle coming from the intake tract as you open the throttle (only while the airflow changes, it's OK on steady throttle). It's a minor irritant which I have already improved by rounding off some of the joins between adaptor plates. Can probably live with this one.
I'm sure there are a number of item's I've left out, but that's the guts of the job described. These EA Falcon throttle bodies are just the ticket when you want an electronic replacement for a carburettor. Be interesting to see how a converted carby 504 would compare with a 504 TI. Would be surprised if it didn't end up with both better performance and economy.
Have fun,
Rob.
For the last 20 years or so the car had run a Holley 320 carburettor -- an improvement on the Solex setup, but nothing to get excited about. It now has a Megasquirt II ECU running MS2/Extra firmware controlling an EA Falcon dual throat throttle body injector. Feedback is from an Innovate LC-1 wide band controller with a sensor fitted in the LHS pipe. At the back I have a 505 fuel pump drawing through a cartridge type 10 micron fuel filter.
Doesn't sound like it'd be all that much work, but the Devil's in the details and the job has called for more than a few moments of musing how to make things work or make them fit. On the whole though, I'm very happy with progress, though there are still a few things to sort out yet.
So, here are some photos and a bit of running commentary.
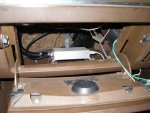
Megasquirt behind the glovebox
The photo is foreshortened, and doesn't get it across, but the MS is mounted on a cradle I made and is waaay far away. There is plenty of room for the original cardboard glovebox to slot back in. You can see the main MS DB37 electrical connector on the left, and the MAP sensor vacuum line looping around it. On the right is the RS-232 connector. The brown wire is the spare analog output from the wideband which I might hook up to an AFR gauge (maybe fit in the ashtray slot which, being built to accommodate French smokers' tastes, would easily be large enough for two gauges).
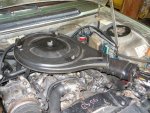
Engine bay overview
Engine bay with everything in its proper place looks reasonably stock. The Ford air cleaner doesn't look out of place and the wiring isn't too much of a rat's nest. Mind you, the Ford air cleaner took quite a bit of adapting to fit. The Ford TBI was towards the front of the engine bay. Since the 604's second carb was mounted near the back, just turning the filter around and relocating the snorkel was my original plan, but the filter ended up at a crazy rakish angle when I tried it. So it was a cut and reweld job which worked out OK (as long as you don't look too closely).
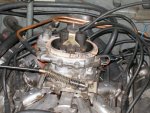
TBI detail
I've mounted the TBI on a bit of 1/4" stainless plate with four studs. This plate bolts to the previous Holley adaptor plate which in turn mounts to the manifold through four recessed allen screws. This two plate arrangement was necessary as the Solex and TBI mounting holes overlap but don't coincide. This sandwich has left the top of the air filter pretty close to the bonnet. I haven't measured with plastigage (OK plasticine); it's not rubbing but it's close.
I bent up 5/16" copper pipe to feed fuel and take away return. The thing flows like a garden hose, so there is plenty on tap. You can see the two injectors front and centre. There are two TPS sensors on the other side. Only using one; I guess the Falcon uses the other for something like idle feedback or some such. Throttle was a bit of a conundrum. I ended up using the original Falcon ball and socket connection so I could use the compression return spring. Rigging up an extension spring for throttle return didn't look straightforward ('cause it needed to go round a corner). The throttle stop is the somewhat jury rigged bit of steel mounted on RHS in the photo. Could do with a bit of stiffening up.
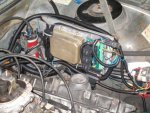
Relay board detail
Left to right we have a shiny red Bosch GT40 coil, then, mounted on a bit of bathroom trim aluminium, Innovate LC-1 controller, Bosch electronic ignition trigger box (ex Volvo) and Megasquirt relay board which gives a single point to draw all connections together. At the bottom of the relay board you can see the DB37 connector which sends a chunky cable through the firewall to the ECU. The knot of wires further to the right is the relay and thermostat for the cooling fan which has been on the car for years. Will probably get the MS controlling this and get rid of the old thermostat.
The Bosch coil seems to deliver enough sparks for me and has no bother starting the car. The ballast resistor had been playing up so a full 12V coil took that out of the equation. I have a spare Volvo dizzy and may lock it up and use the MS for full ignition control to see how that goes.
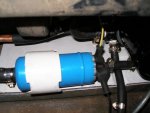
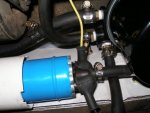
Fuel pump/filter
Two shots of this because I was too lazy to jack the car up and snap from further away. This is on the LHS in front of the rear crossmember behind the rear passenger footwell. I made up a mild steel mounting plate and drilled holes to mount it to the footwell. Then I was able to position everything on the bench without having to lie under the car.
On the left is a large copper pipe feeding a 1/2" hose to the inlet of the pump. The fuel filter is the shiny black thing on the right. Somewhat unconventionally, the pump draws through the filter which allows the filter to do double duty as a surge tank. I did this because I didn't want to be fitting a 1/2" outlet to the fuel tank. The pump requires a large inlet because it uses the fuel for cooling. The worry was that the fuel would get hotter and hotter... but that doesn't seem to eventuate (phew). There are four connections on the filter: from tank, to injector, injector return, return to tank. I didn't use the original tank return line because it (strangely) returns at about the 1/3 full level in the tank. I sent the return up to the breather at the top of the tank and have a check valve in the line so we don't draw air down this line. Since the return line should mostly be returning air accumulated at the filter, this seems satisfactory.
The fuel pump plumbing was in many ways the most complicated part of the setup. Pretty happy with it though. Despite the apparent tangle of hoses, nothing is actually rubbing on anything else and, in the flesh, it doesn't look any worse than the 604TI's pump and filter arrangement in the workshop manual.
Not pictured is the coolant temp sensor (tucked in to the valley in place of an existing temperature based vacuum switch), or the air temp sensor (a thermistor put in a drilled out old plastic medicine bottle, cable tied behind the front bumper).
So, how does it go? To begin with, I was astonished that, not only did it start first time, but it idled (at a very lumpy 450rpm or so). Definitely a promising beginning. I haven't yet finished tuning (waiting for the Christmas madness on the roads to abate), but the car has already been transformed. It still has all the stately graces a 604 should have, but the old dead areas of unresponsive throttle have gone. If you move your foot on the throttle, you are left in no doubt that the engine has got the message. Of course it's still no fire breathing monster, but it is really pleasing to feel it so responsive.
The other thing about the performance is that it's willing when cold (well, overnight in Sydney isn't exactly cold at the moment, but the car certainly used to be sluggish untill fully warmed up).
It'll be a while before I have economy figures. Obviously the consumption isn't going to be at its best while I'm tuning, but I'm hopeful that the economy will be very much better with mod cons like EGO feedback to help it out.
Problems
Yes there are still several problems to iron out. The biggest problem is the noise from the fuel line. Because I'm drawing through the fuel filter, there is just a 2" length of hose between the pump and the original steel line which is mounted direct to the floorpan. Every little pulse from the pump is turned into magnificent high fidelity sensurround sound with the passenger compartment making a wonderful soundbox. For the moment, I've left the fuel lines dangling, still noisy, but at least the banshee is a bit less amplified. My plan is to put a blind vertical pipe between the fuel pump and the fuel line This pipe will have air at the top which should work as a poor man's (or cheapskate's) accumulator, evening out the pulses. Kinder to the fuel line, and to my ears.
Probably the next biggest problem is the throttle throw. Having mounted the cable to the ball/socket connector, it only needs to move about half as far as the old Holley did. Consequently, the pedal is about 1 1/2" from closed to wide open. This has already led to a couple of cases of unwanted wheelspin, which is just not in keeping with the 604 image. I plan to move the pedal pivot up a couple of inches to increase the throw, but it's acceptable for driving at the moment.
I'm running full manifold vacuum (not ported vacuum) to the distributor advance unit. This seems to be working OK and I haven't had problems with pinging on take off. The engine does seem to stay cooler too, but I'm keeping a watching brief on this score.
The other problem is a whistle coming from the intake tract as you open the throttle (only while the airflow changes, it's OK on steady throttle). It's a minor irritant which I have already improved by rounding off some of the joins between adaptor plates. Can probably live with this one.
I'm sure there are a number of item's I've left out, but that's the guts of the job described. These EA Falcon throttle bodies are just the ticket when you want an electronic replacement for a carburettor. Be interesting to see how a converted carby 504 would compare with a 504 TI. Would be surprised if it didn't end up with both better performance and economy.
Have fun,
Rob.