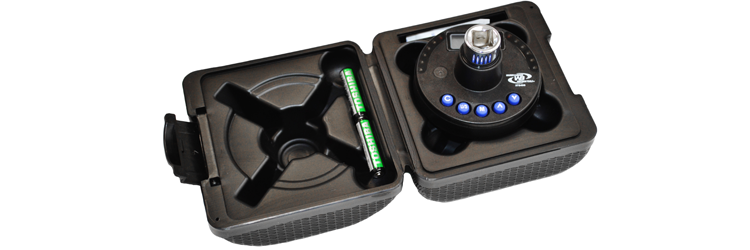
How to Understand Angular Torque and Torque to yield?

Not pale enough ...You don't say!
Hi.Thirdly the idea that it is verbotten to ever reuse a TTY bolt is part of the myth of the world "yield". The bolts are quite capable of yielding a 'long way' before they suffer any local area reduction and get to necking and danger of failure. Most manufactures do give a length measurement under the head for safe reuse. I have reused head bolts and crankshaft pulley retaining bolts and had no failures. A good clean and detailed inspection and measurement will be required. But that does not say you should do it !
Jaahn
Wippet good questions. To answer the last first then yes probably safest to spend more money and get new fastners !! Possibly made in some cheap asian or european backwater but who knows the quality of the steel and the production.Hi.
Interesting to know of your prior experience. There are some clever, experienced members on this forum across a range of disciplines.
Interesting PP pages. If the speaking notes were available that would assist to understanding some of the graphical information.
How would one know if a bolt is used in the elastic range compared to the plastic range, for a particular application? Maybe torque wrench for elastic, and initial torque/angle turn for plastic?
For the average mechanic in a critical torque to yield application eg: conrod, mains, cycl head etc might it be safer to just replace the fasteners?
Cheers.
Quality rod bolts such as ARP2000 or 625+ are done that way. I use a rod micrometer and typically stretch a 5/16” bolt 0.0055”.Interestingly in the old days some British motorbike bigend bolts were tightened to a stretched length using a micrometer on the length of the bolt. This also gave a set preload independant of torque or friction but was not into the plastic range. I believe some critical aircraft bolts were normally tightened similarly to a specific measured stretch.
Jaahn
Hi.Quality rod bolts such as ARP2000 or 625+ are done that way. I use a rod micrometer and typically stretch a 5/16” bolt 0.0055”.
Oh, what fun. Inches and foot poundy. Yard stick shit.
I’m gone.